- >> Company Profile
- >> President's Speech
- >> Brand Service
- >> Mission & Goals
- >> Value System
- >> Brand Construction
- >> Philosophy and Mode
Address: Room 614-616,China World Office 1, No.1 Jian Guo Men Wai Avenue, Beijing, P.R.C.
Tel:+86-10-65051177
Fax:+86-10-65058988
E-mail:soongs@soongsart.com
Home >> Show Items
Yongle Large Longquan Tray Incised with Peony Pattern in Ming Dynasty D:36.6cm
![]() |
![]() |
According to the record of “porcelain” in 194th volume of “Collected Statutes of the Ming Dynasty”, the provisions in Hongwu Year 26 pointed out that if people wanted to produce wares, they had to make clear the model and calculate the craftsmen and materials. If the number of the wares was too large, the craftmen shall be sent to the capital for working in the new kilns. If the number was not large, it could be produced the wares in Rao, Chu and so on. This literature mentions Jingdezhen Kilns of Raozhou and Longquan Kiln of Chuzhou, which produced porcelain for the court. According to the provisions, the form and pattern of the porcelain shall be determined by the court. Thus, the porcelain in the two kilns shared the same pattern. Only the incised picture under the glaze layer for the porcelain in Longquan was different from the various decorative methods for the ones in Jingdezhen. Those reflect the passion of the emperors in the early Ming Dynasty on the porcelain art. Under the management of the court, Longquan and Jingdezhen produced the porcelain with different ways and decorative methods. They shared the same goal and the style of their porcelains were the same even though the two kilns were far from each other, which was an interesting phenomenon in Chinese ancient porcelain history. This kind of Longquan wares shared the same quality and status with the ones produced in Jingdezhen Kiln in the early Ming Dynasty.
The tray is one of the examples, which saw the interested and complex history. It has large dimension, straight mouth and are-shape body. The peony patterns are shallowly incised at the center of the tray. Lotus pattern is engraved on the outer wall of the tray. The way of engraving is smooth and well-arranged, which achieve the art effect of line and surface. The peony has always been regarded as the most elegant flower just as an old saying “Peony is the flower that represents wealth”. This kind of pattern is classical in large trays with green flowers of Jingdezhen Kiln. Apparently, the form and style of the tray shall be determined by the court as the ones in Jingdezhen. Its outer wall has pure color without any pattern, which fully reflects the beauty of glaze. The glaze is green and it looks delicate. The ring foot is made up of glaze. The foot is smooth and thick, which represents the nobleness. The condition of the working procedure for the base burning ring of the immature molding bed can directly reflect the features of “official porcelain”. As for the high-grade “official porcelain”, the connection of inside and outside of immature molding ring and the glaze is clear and distinct. The visual effect of the porcelain is integrated just like a jade ring. The tray is one of the examples. The burning method of immature molding ring for the trays and bowls in Longquan Kiln aimed to realized the goal that the glaze can fully cover the ring, the effect of which was to inherit the nobleness of Ru Kiln in Northern Song Dynasty. In the early of Ming Dynasty, the court still applied this technique and strictly followed the working procedure to make the bottom look graceful. Thus, the turning of the immature molding bed ring is handled carefully and looks neat, which is the remarkable symbol of high quality at that time.
Although people know that this kind of high-grade porcelain is produced in Longquan Kiln, the concrete position of the kiln is still unknown and the corresponding remains cannot be found. Thus, whether the porcelain belonged to the “office” or “civilian” is still unclear. In recent years, the concrete position of the kiln is found at the “Fengdong Rock” in Dayao Village of the present Longquan City after research and excavation. The people who find out this place call it “Longquan Official Kiln of Chuzhou in Ming Dynasty” (Refer to “Discovery: Longquan Official Kiln of Chuzhou in Ming Dynasty” written by Ye Yingting etc. and published by Xiling Society of Seal Arts Press, 2005. “Unearthed Porcelain at the Kiln in Fengdong Rock of Longquan” edited by Institute of Cultural Relics and Archaeology of Zhejiang etc. , Cultural Relics Publishing House, 2009.) The porcelains remained in the kiln share the same pattern with the ones in Jingdezhen Kiln of the same period. In addition, the handling of the porcelains that were not chosen is the same as the factory of Jingdezhen in the early Ming Dynasty. Thus, Longquan Kiln can be demonstrated to be the official kiln.
The tray is the porcelain produced for the court in the early Ming Dynasty. This tray played a key role in the culture exchange of Ming and the mid Asian region. It can be found today, for it was popular as the award given by the central government and became the collections among the local noblemen. The collections in local region were mainly about the porcelain of Longquan. The one with the same shape and quality of this tray is the [green glazed tray incised with grape pattern produced by Longquan] collected by the Turkish Topkapi Palace. The glaze on the two trays shares the same effect and the handling of immature molding ring is unified, which can indicate their age and quality.
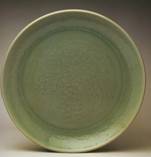
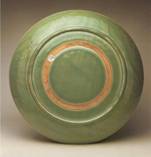
(Picture) Green Glaze Tray Incised with Grape Pattern Produced by Longquan in the early of Ming Dynasty, the collection of Turkish Topkapi Palace TKS15/218